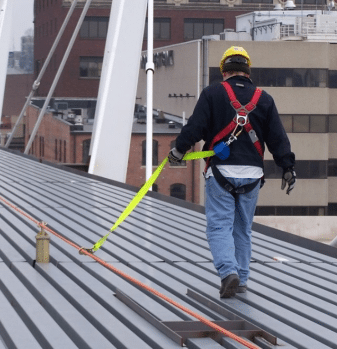
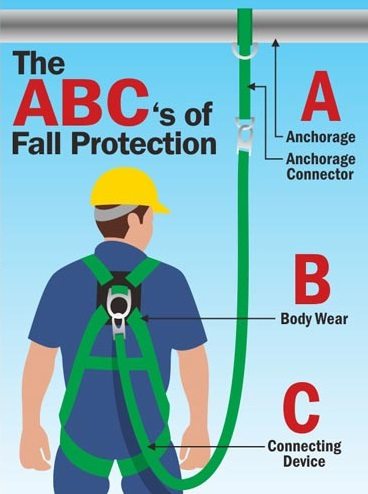

Topics on this page:
Fall Protection and Restraint
Death and serious injuries resulting from falls happen every day in workplaces around the country. Anytime you are working in a situation where you could fall four or more feet, some sort of fall protection system is required. There are a number of different types of fall protection options, the type selected will depend on the nature of the job and the area where work is happening.
State of Washington’s Department of Labor and Industries requires EWU to provide adequate training for employees who are exposed to fall hazards in the workplace. Training employees in Fall Protection and Restraint is required when any of the following conditions are met:
- New employee(s) requiring Fall Protection & Restraint in their job duties and annualized refresher training thereafter
- Reasonable belief an employee does not have adequate knowledge of operations and/or does not display competency or skill appropriate to the work environment
- Changes in the workplace environment to perform work safely
- Any equipment used for EWU Fall Protection and Restraint has changed; or is being used in a manner inconsistent from the manufacturer’s recommendations
If any of the previous conditions are exhibited, work must be stopped by a supervisor acting as a qualified person, or by co-workers currently trained as a competent person.
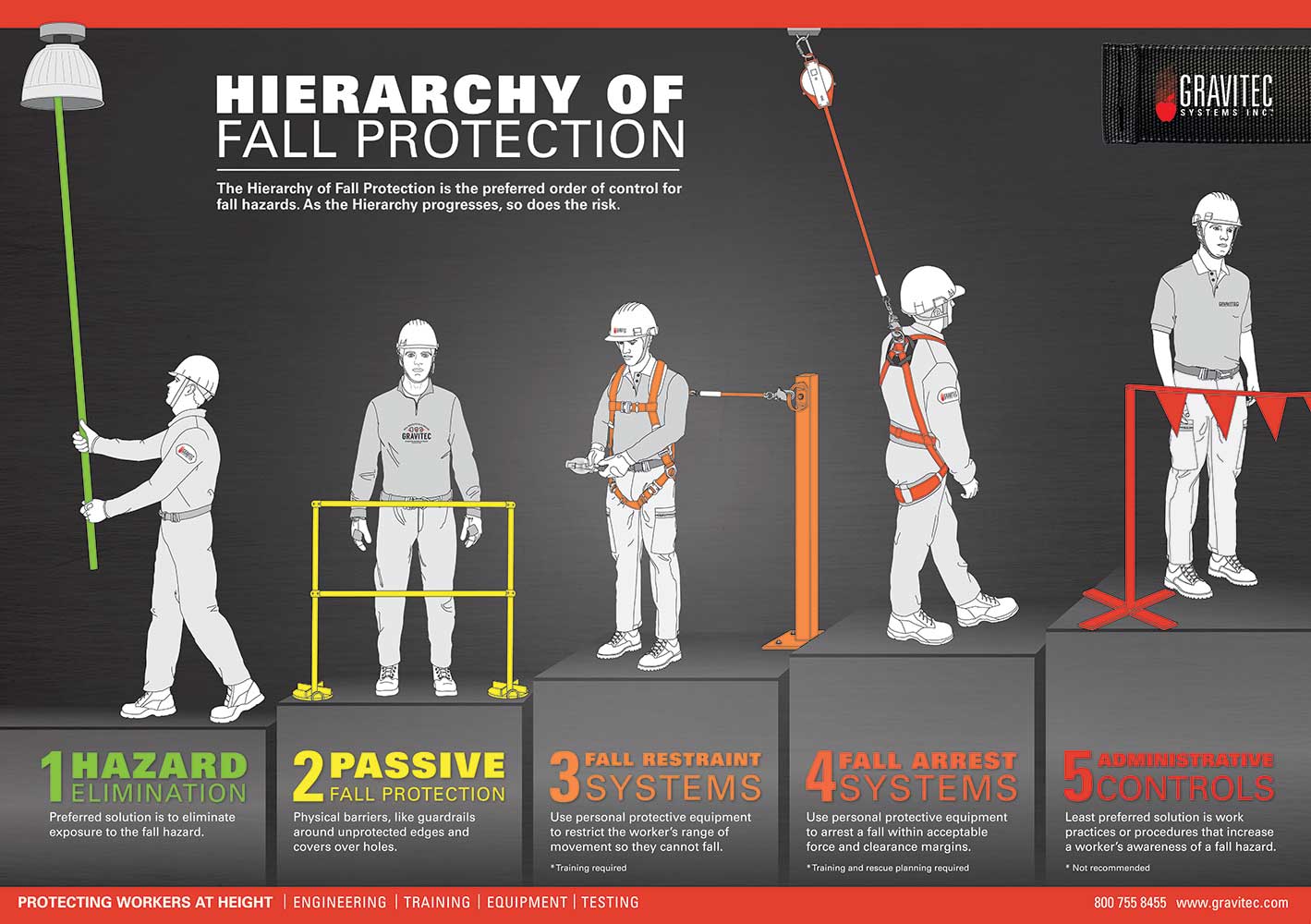
Washington state revised rules for unified fall protection require workers to use fall arrest or restraint above or adjacent to dangerous/hazardous equipment, excavation/trenching efforts, rescue/recovery, and elevated work at four (4) or more feet in all workplaces.
Existing workplace standards remain for elevated work at ten (10) feet or more for those engaged in roofing, leading edge work, rebar forming or iron work, or work using scaffolding.
When engaging in fall protection and restraint work activities please refer to EWU’s Fall Protection and Restraint program for general requirements for supervisors and employees. If you are a qualified person supervising work, or working as a competent individual at working heights over ten (10) feet you must complete a Fall Protection Work Plan and notify the EWU Facilities Operation Manager and the EH&S Department before elevated work begins.
All equipment must be thoroughly inspected before donning any fall arrest, fall restraint, or positioning equipment. The inspection must verify that the equipment to be used is in good condition. Review and complete fall component inspection forms prior to use of equipment. Keep completed inspection forms on file with your supervisor for the life of the device.
Fall Protection and Restraint Program
This program outlines the general EWU procedures for fall protection and restraint. Employees are required to follow this program if they work:
- Above or adjacent to dangerous/hazardous equipment
- In excavation/trenching
- In rescue or recovery
- Elevated at or above four feet
Fall Protection Forms and Procedures
This form must be used to document any training provided to employees or students. This form should be attached to any handouts or presentations given as part of the training. Training records must be maintained for a minimum of three years. Send all training records to EH&S annually to ensure appropriate retention.
This form must be filled out by the installer after the installation of an anchorage connector and by the employee prior to using the anchorage connector each day.
A Fall Protection Work Plan must be in place for any work with a fall hazard above 10 feet. The plan must be completed prior to the start of work and must be readily available at the work site for inspection.
This form must be filled out by the employee prior to donning a harness to document that they have fully inspected the harness for defects. If the harness will be used multiple times in one day, fill out the inspection form once at the start of the day.
Horizontal Lifeline Inspection Form
This form must be filled out by the installer of the horizontal lifeline after installation and by employees prior to each day’s use of the horizontal lifeline.
This form must be filled out by the employee prior to using a lanyard to document that they have fully inspected the lanyard for defects. If the lanyard will be used multiple times in one day, fill out the inspection form once at the start of the day.
Standard operating procedure for rope terminations used in fall protection.
Self-Retracting Lifeline Inspection Form
This form must be filled out by the employee prior to using a Self-Retracting Lifeline (SRL) to document that they have fully inspected the SRL for defects. If the SRL will be used multiple times in one day, fill out the inspection form once at the start of the day.
Vertical Lifeline Inspection Form
This form must be filled out by the installer of the vertical lifeline after installation and by employees prior to each day’s use of the vertical lifeline.
Fall Prevention & Protection Resources
Elevating Work Platforms & Aerial Lifts
There are three types of aerial lifts available at EWU.
- Boom lifts
- Scissor lifts
- Personal or Pod lifts
Aerial Lift training is required for anyone who uses a lift. Training must happen before the lift is used and must be renewed every three years.
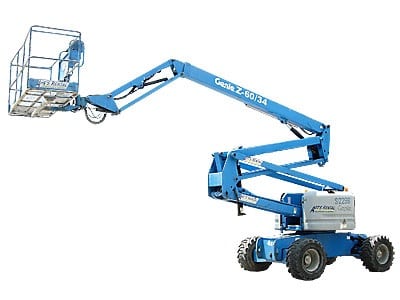
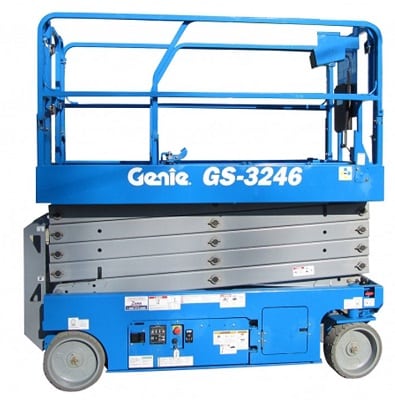
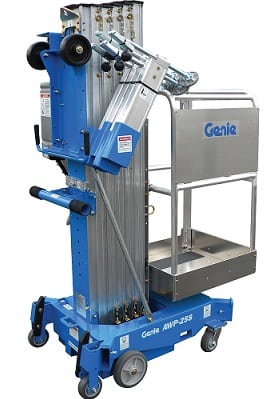
Always read through the operator’s manual before operating a new lift. Lifts are required by law to have the operator’s manual on-board during lift operations. Never operate a lift that is missing its manual!
Follow the EWU Procedures for Checking out Manlifts when a lift is needed. Each lift will come with a clipboard that contains the inspection checklist
Pre-Operation Check
Before using an aerial lift, you must do a complete pre-operation check. Follow the checklist on the lift’s clipboard.
Lift Inspection
The first part of a pre-operation check is to inspect the lift. Use the checklist and the operator’s manual to inspect each part of the lift for proper function.
- Make sure all signs are present and legible and that the operator’s manual is present.
- Check
- Tires,
- Fluid levels,
- Engine,
- Battery (if present)
- Lights, guages, and alarms
- Lower and upper controls
- Emergency lowering
- Mechanical fasteners and locking pins
- Cable and wiring harnesses
- Outriggers, stabilizers, or other structures
- Guardrails
- Steering and brakes
Never operate a lift that doesn’t pass the inspection.
Work Zone
Make sure to clear the work area of unnecessary people and block off the area to walking and vehicular traffic.
Most lifts require relatively flat ground in order to operate safely. Before using a lift, inspect the area where it will be used.
- Check the ground to be sure it is flat and packed, loose ground may not support the lift.
- Look for potholes or divots that could destabilize the lift.
- If the work zone is on an incline, check the operator’s manual to make sure the lift can operate safely on the slope.
- Remove any debris in the work area.
After inspecting the ground, inspect the area overhead.
- Look for power lines and other cables running over the work zone
- If the work zone includes power lines, make sure to identify the amount of power traveling through the lines and maintain a proper distance based on the power.
- Look for other overhead obstructions, like tree branches and roof overhangs.
- If working indoors, check the ceiling height and look for areas where the height changes.
Aerial Lift Fall Protection
Boom lifts always require the lift user(s) to wear fall protection. Every person in the boom lift must wear their harness and their lanyard must attached to one of the approved tie-off locations. A separate tie-off location must be used for each person in the boom lift.
- Refer to the operator’s manual for approved tie-off locations.
Generally scissor and personal lifts do not require fall protection, as long as the guardrails are in place during use and all personnel remain inside the guardrails. Fall protection would be required for:
- Everyone one in the lift, for any procedure that involves the removal or opening of a guardrail
- Specific individuals, for any procedure that involves a person leaning out over a guardrail
The lanyard used for fall protection must ensure that the worker will not:
- Free fall for more than six (6) feet
- Contact any lower level
Weather & Aerial Lifts
Weather conditions can create hazardous environments for lift use. Lift users must take weather into considerations when planning outside jobs. Always check the operator’s manual to determine safe lift use for different weather conditions.
Never operate a lift during lightening storms!
Wind
All lift operations must be terminated if wind speeds at the work height reach 20 mph. Manufacturers may have requirements to terminate work at lower wind speeds. There may also be height and weight restrictions for the lift at higher wind speeds.
Remember that wind speeds on the ground will be lower than the wind speed higher up.
- Consider postponing tasks when wind speeds are in the 15-19 mph range.
On windy days, check out an anemometer with the lift and use it to monitor wind speeds.
Extremely Cold Weather
Both lifts and personnel can be affected by cold weather.
- Lift hydraulics can be impaired at extremely cold temperatures.
- Lifts may have reduced weight capacity as temperatures drop, check the operators manual.
- Lift battery life may be reduced in the cold.
- Lifts may be slower to respond at cold temperatures.
- Personnel may have a harder time operating lift controls under cold conditions. Cold weather clothes can limit dexterity and exposure to cold can compromise response times.
Lift Operator Forms and Procedures
Aerial Lift Pre-Inspection Form
Use this form to document the safety inspection of an aerial lift before you operate it. This form should be kept in Rozell with the lift clipboard when the lift is returned.
EWU Procedures for Checking out Aerial Lifts
This document has all the steps needed to check out and return aerial lifts at EWU.
Lift Operator Personal Equipment Use Log
Lift operators should use this form to record the types of personal lift equipment they use and how many hours they spend on each type of equipment.